Posted on Wednesday August 14, 2024
Improving Efficiency in Our Warehouses
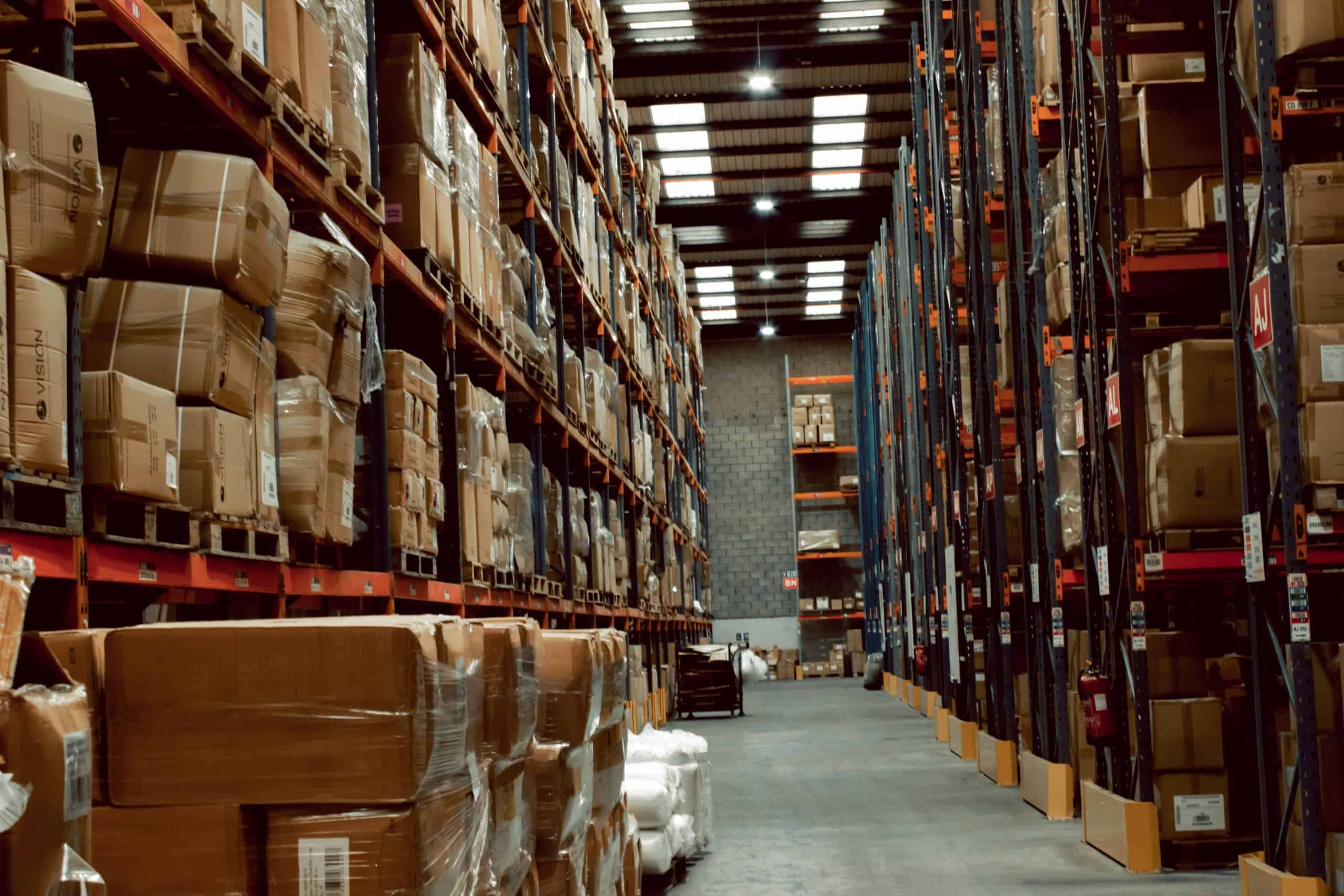
Vision Linen’s Headquarters in Blackburn hosts 85 staff members and the complex of buildings includes two warehouses with 137,000+ feet of space and 30 team members.
In 2023 Warehouse Manager Gavin Clarkson came onboard to help increase the efficiency of the warehouse sites and with the assistance of Warehouse Supervisors, Ian Hartley, Allan Weeks and Jason King they have spearheaded a campaign of improvements that has led to incredible results including improving the On Time In Full (OTIF) rate from an average of 71% in 2022, 95% in 2023 to 97% YTD in 2024. That’s a 26% increase on OTIF to the customers. Added to that are the increase in sales orders, which highlights the OTIF scores further.
2022 – 32243 sales orders
2023 – 50648 sales orders
2024 – 38917 sales orders YTD
When asked about how the change process came about Gavin Clarkson said “I’m a big believer is getting ideas from the shop floor. It shows you’re listening, and the people on the floor know the process best. Taking that input helps morale so people enjoy work more!” With the assistance of suggestions from the entire warehouse team, £160,000 of improvements have been made thus far with further works on the way, mainly around H&S of the staff & site.
Already completed items include the removal of excess items in storage so the full space can be utilised for production work, replacing racking and netting for safer and more efficient storage, and clear floor markings for FLT laneways and storage spaces to provide visual indicators. Shipments have also been rearranged and marked out so that delivery partners and shipment days are grouped together for better accuracy during pickups and better on-time rates.
Order sequencing has been put into place to improve replenishment and picking speeds. This included adjusting the types of patterns possible so side to side picking can be implemented to reduce travel time with trollies used to increase speed. Packing tables now include onsite rework areas.
Ian Hartley, who came from an ecommerce background, also brought in additional Sunday shifts to help with weekend online orders. This has helped to ensure that next day and two-day shipping is executed more reliably. When asked how he approached the warehouse improvements Ian said “We need to try things and learn from mistakes to keep improving. We looked at how many team members were doing non-production work and why, then we tried to work on reducing that so they could get back to doing that production work.”
These improvements have meant that daily picking has increased by up to 300% and monthly orders picked by 250% with no additional staff. Packaging sourcing has also been looked at to utilise multiple suppliers which has reduced costs by 40%.
Improvements still in progress include new lighting for better all-season visibility, packing table layout evaluation to improve speed, and moving ecommerce shipments to the new Salford site acquired with the acquisition of Swiscot Textiles so the Blackburn warehouses can focus on contract fulfilment.